Hybrid Drive Wear - Naval Yachts Refuse To Honor Guarantee (Again).
- Chris Leigh-Jones
- Feb 15
- 5 min read
Updated: Apr 25
Last week, we spoke about "less is more" in that particular example, removing an overabundance of shims used to align the drivelines on Vanguard. The nature of such work demands close attention, which can often reveal the onset of other, more subtle problems. So here is that story:
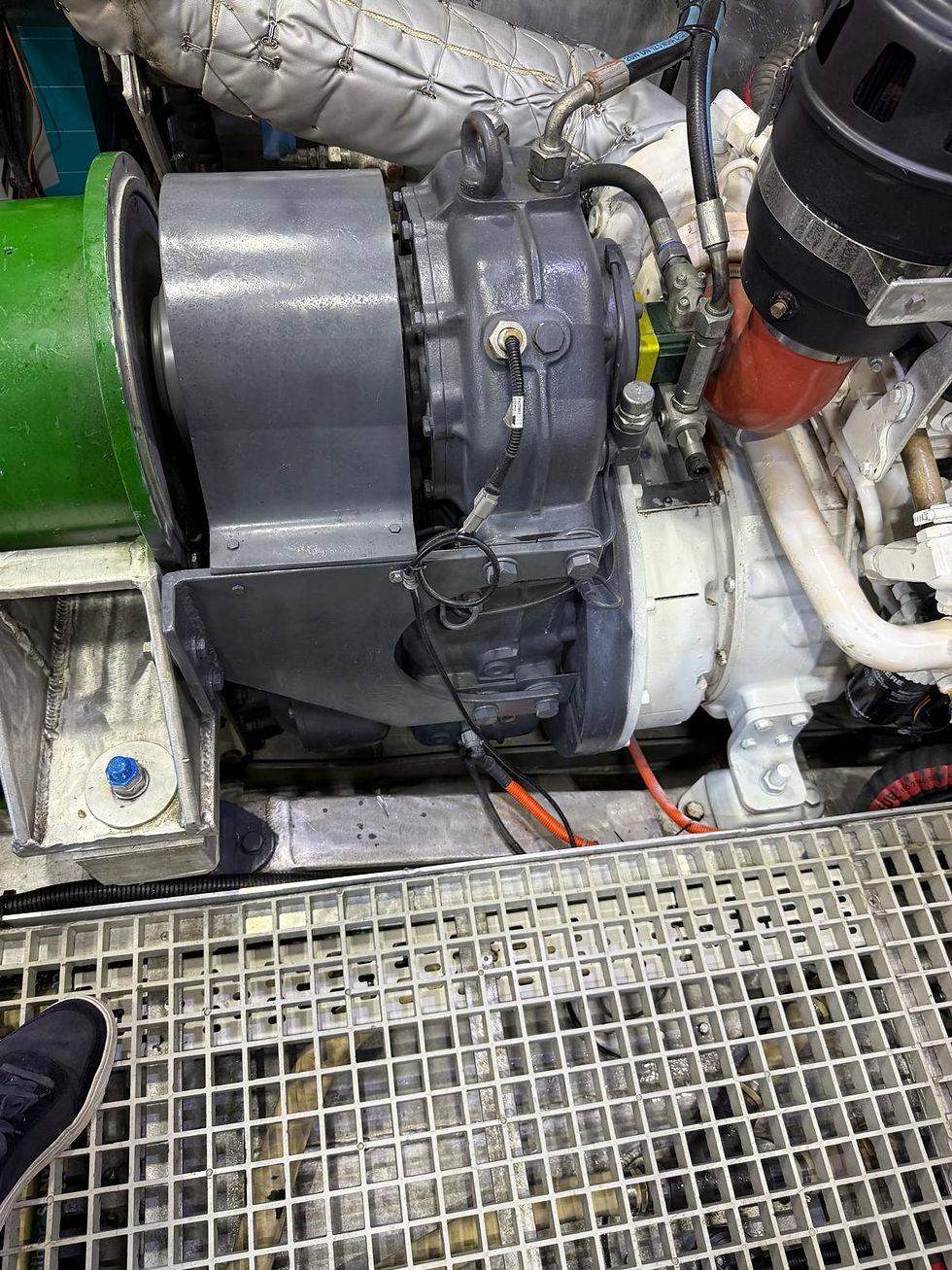
Our hybrid E-Motor drives consist of three hefty assets: a 30kW E-Motor from Praxis Automation that doubles as a motor and generator, a coupling, and, thirdly, a step-up gearbox (PHT) from Esco Power. After fixing a few initial hiccups, these robust components performed well, and charging at 30kW is a blessing in quiet anchorages. Vanguard's design boasts impressive redundancy for its mission, which can create a false sense of security— a repeated mistake adds no security.
While realigning the drives, we discovered a surprising backlash in the port engine Hybrid drive coupling. Since the drive is bidirectional, we shouldn't have seen any backlash. With a stroke of luck, we had time for a strip-down, which led us to share our findings with Naval Yachts and Esco Power. Esco Power responded promptly and worked with us to find a solution. Naval Yachts installed the unit; however, they immediately opted for the blame game, which was unsurprising, given previous experiences. Hope springs eternal, or so they say! (We subsequently stripped the Stbd drive to find similar but less extensive damage attributable to the same reasons.)
So, what went wrong? Well, three issues stood out:

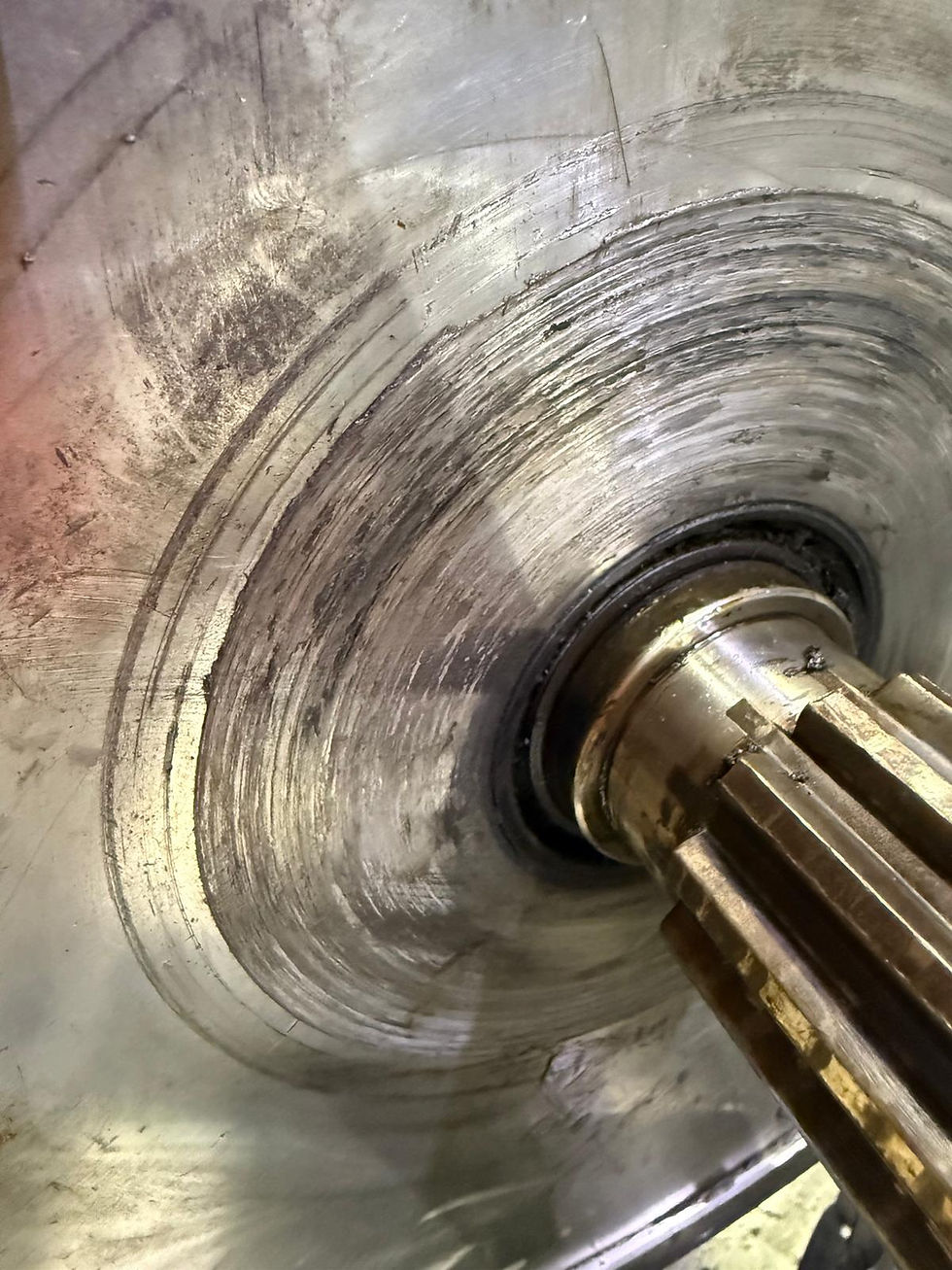
1. Construction supervision.
Naval Yachts (or their subcontractor) used a cold chisel instead of the specified tool to tighten a retaining lock ring. As a result, it wasn't fully locked in, allowing axial movement and leading to some lovely metal-on-metal fretting at the drive end.
2. Machining mishaps.
The splined connection to the E-Motor was noisy and didn't meet the specified standards per drawing DIN 8420. It was tight initially, but everything loosened up when under load, which is always a great way to keep things interesting.
3. A classic case of 'close enough.'
A design flaw meant that the E-Motor end of the coupling could move forward but not back, relying on the E-Motor casing to keep it in check. That genius design idea resulted in scoring, heat buildup, and a nice little vibration show.
Most problems have multiple solutions, so work with what you have. We first consulted Esco Power about the issues, and their technical support agreed with our assessment. We also spoke to the shipyard in Fort Lauderdale, Yacht Management of South Florida, for local machine shops, ultimately landing on Tropic Machine and Fabrication. We kept Naval Yachts in the loop, but they immediately played their predictable blame card—a lesson slow learned.
Implementing a repair.
Starting at the PHT drive, the output is taken by a connecting flange driven via a splined output shaft. The backlash was minimal (Esco Power had machined both components). We added molybdenum disulfide anti-fretting paste to the splines before reassembly. Additionally, we procured new Nylock retaining nuts and torqued them to specification with the help of a newly made dedicated assembly tool.
Top Row - Naval Yachts assembly using a cold chisel on the nyloc nut, damage to nut, red coloration on splines from fretting damage.
Bottom Row - new nut and purpose-made assembly tool. Clean tight assembly with no backlash.
Welding the hefty shaft retaining washer to the splined E-Motor coupling will prevent axial movement of this component. Previously, all damaged surfaces had been dressed and trued to the axial dimension. The coupling was reassembled onto the E-Motor shaft using Loctite 660. This was not a preferred choice but was necessitated by the level of wear on the splines. An alternative was to re-machine those splines, entailing approximately a 4-6 weeks delay. We used a small washer to ensure clearance from the motor casing, then torqued the M10, Class 12.9 Allen screw to 95NM before letting the Loctite set up overnight.
E-Motor end coupling, before Top, after Bottom. We had about 0.3mm play and used Loctite 660 as a semi-permanent securing compound to prevent backlash and ongoing fretting.
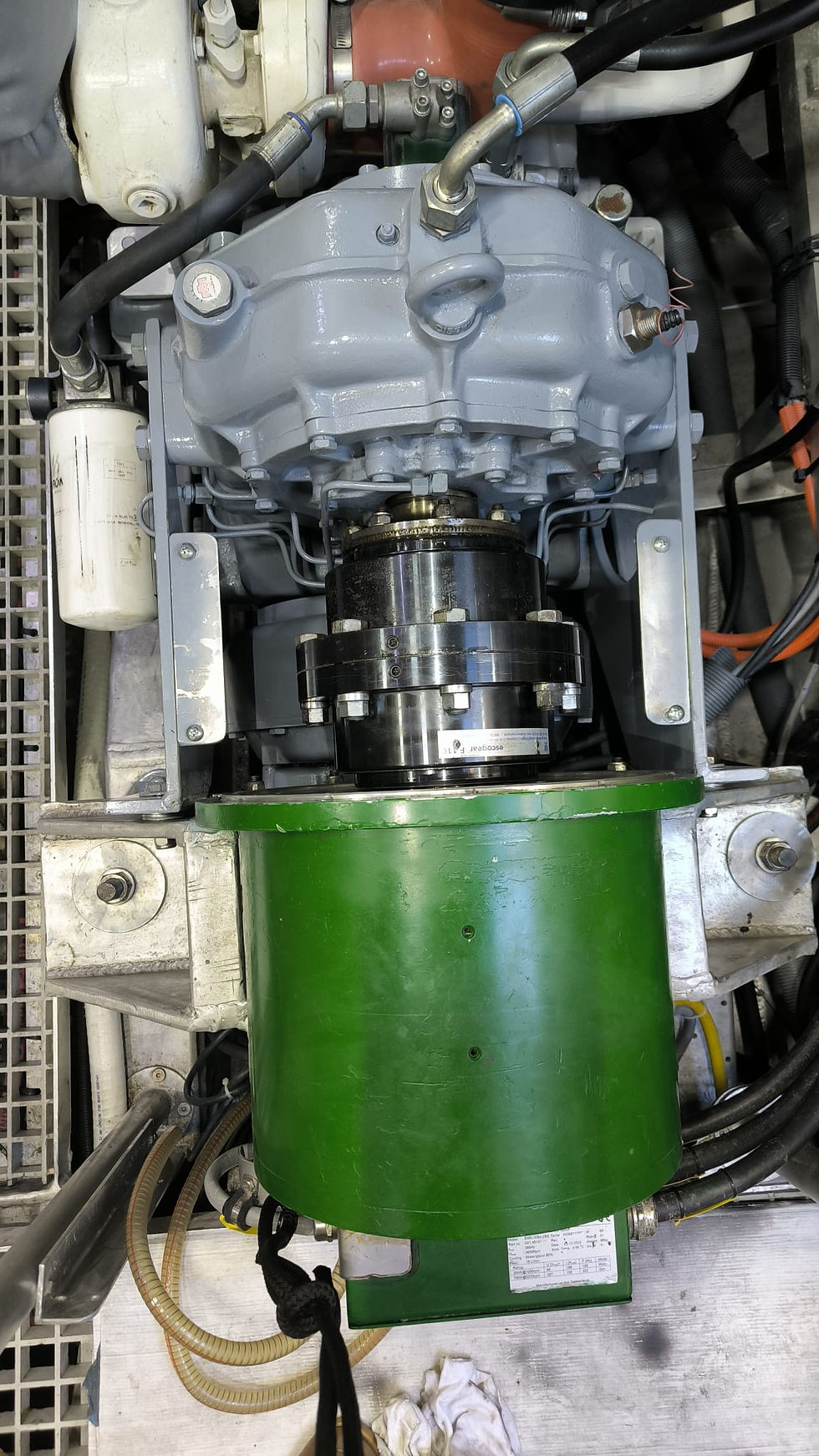
Loctite 660 is designed to retain worn splines and keyways on shaft lines. It is a permanent solution but can be removed by heating to>240 deg.C. Once set up, a we confirmed concentricity before the Loctite could cure fully. The e-Motor was replaced. Next we realigned the E Motor to the PHT drive, this necessitated lifting the E-motor support cradle to remove shims as the alignment has initially be set wrongly, (no surprise there).
We will test the completed assemblies next week when the exhaust modifications are also completed. If this does not work as intended, Plan B is to replace the coupler assembly with a flanged rubber industrial motor drive coupler. 30kW at between 1000 and 3200 RPM is quite a low torque requirement, so it should be an easy swap out that we can complete in Charleston, SC.
A shout-out here for the engineering assistance provided by Zach, Ceaser, and the team at Tropic Machine and Fabrication. 72 hour turnaround!
web site: www.tropicmachine.com
Now, does Naval Yachts (Antalya) stand behind their work after only 300 hours of operation?
I typically avoid negative comments, preferring to focus on outcomes and the journey. However, one observation about Naval Yachts is well overdue. Dincer Dinc, Technical Director and co-owner is steering this process. Over eleven months since the chaotic delivery of an incomplete build and through a detailed rebuild at our own expense, we come to realize that Naval Yachts "Guarantee Policy" is a marketing stunt; it will not be honored and has zero value.
On a brighter note, Vanguard has now been approved independently by UK MCA as seaworthy - Category (2) at our own effort and expense, despite this behavior from Naval Yachts.
When the remaining repairs are completed, we will ride the Gulf Stream north to Charleston (against a northerly wind, if there is one, letting the seas stack up). That should be a worthy test of the upgrades. Caveat Emptor, folks!
Lastly, this morning I woke up early, 5.30 am as usual; this was the view that greeted me from my cabin. You have to love Fort Lauderdale.

Yesterday, I received an email from one of our subscribers asking if this experience was a one-off. A difficult client can easily contribute to problems in a long-term build. In answer, I met three other clients of Naval Yachts during my time building Vanguard. Owners of XPM 78-1, XPM-85, GN-47. I know the story of each. Below is the contact for Naval Yachts, Baris, and Dincer Dinc. Perhaps write to them and ask for a reference from these specific clients?.
Barış DİNÇ <baris.dinc@navalyachts.com>
Dinçer Dinç <dincer.dinc@navalyachts.com>
Oh, and while you are labeling, label that tool ! I have found numerous things on my boat that would have been a complete mystery without the label that some kind soul put on years ago.
I can't find it now, but I read a comment from Steve Dashew where he recommended NOT building a new boat - rather buy a well maintained used boat that has already had the kinks worked out.
Seeing the build issues and bogus guarantees make this ring true.
I am sure there are others that have similar stories with this yard, always look for references. Find the boats they have built via there their youtube or yacht-buoy or where ever and talk to the owners. Find the owners the yard does not provide as references, they are the ones with the stories.
What a horrendous find, Chris! Beautifully repaired by Tropic Machine and Fabrication. I can't believe a cold chisel was used on a new assembly; that's butchery of the first order. And another plug for the guest's suggestion below: that job needs to be permanently tagged in some way. Your ship's manual must be several volumes now...
Speaking more generally now: your experiences with Naval Yachts has convinced me that our next boat will not be a new build—can you estimate how many hours collectively have you and the various teams spent on locating, analysing, and repairing a high-dollar new build? And Naval Yacht's responses over the various problems found has been truly disappointing. Best wishes for the future.
make sure to put some kind of permanent tag or label about that loctite to save someone down the road a headache ! you know the saying - measure twice label once